Table Of Content

Then the pattern is woven into the warp with a fly shuttle, the weaver pounding down the weft with the reed as she goes. Multiple blankets are woven one after the next on the same warp, then cut off the loom, hand-knotted, and washed. For cotton dhurries, the horizontal loom is set with a white cotton warp or taana (hence the white fringe on the ends of our dhurries). Our pattern is woven by hand using a shuttle, and beaten down into the weft with a metal-toothed comb, completely covering the warp, which makes these distinctive flatweave rugs fully reversible. Remove the pins and repeat the process for all of the alternating #2 blocks.
Setting your block printing projects
This will help you keep the block oriented the correct way when printing. When ready to begin printing, fabric is tautly pinned to a table. The artisan then prepares the blocks they will use to print. Made from hand-carved teakwood, the process to chisel the designs into the blocks is an art form in itself, often taking several hours to carve a single block.
Stencil Printing
These days, you’ll find an incredible variety of artworks and textiles created using traditional block printing techniques or heavily inspired by the effect of block printing. Our Mander print is a perfect example of this, and you can see it here in Mustard. If you're using fabric ink for your design, you may need to let it dry and then heat set it after printing.
Related Articles
In this blog post, I am excited to share how to block print fabric. There are multiple ways to incorporate the art of block print in your home. Two key learnings at this stage - it helps to remember that the blocks come out back to front on the surface you’re printing on, especially, ahem, when it comes to letters. And if you press too hard, the edges of the design will smudge rather than be crisp. However, if you used water-based inks then you’ll need to follow the setting instructions that are printed on your ink label.
Block printing is an age-old printmaking practice that stems from many countries including China, Japan, Korea, India and parts of Europe. Of course there’s a lot more to love about it than just that - the projects you can create with it are just seriously endless. The results are a longer lasting block that can be printed again and again though, which is why so many people go that route.
Foil Printing
Pigment printing is the second most common method used in screen printing. In a pigment print, ink is mixed with a thickening agent, creating a paste like substance that sits on top of the fabric. Pigment printed fabrics tend to change the texture of the fabric, creating a slightly firm texture in areas where the ink has been applied.
Step 1: Locate Your Found Items To Print With
Serena Dugan's block-printed designs are imbued with artistry - Business of Home
Serena Dugan's block-printed designs are imbued with artistry.
Posted: Thu, 14 Sep 2023 07:00:00 GMT [source]
This would be especially helpful if you’re concerned about messing up and carving too closely into something. But for highly detailed areas, you’ll probably want to use the smallest size (#1). I often use the largest size to carve out larger areas, so it goes a little faster.
You want as many pixels as possible to be a part of the same object in your scene, which means that your photo is relatively close-up. If objects in your scene start to be smaller, they may only be one or two "dotscreen cells" wide, which means zero definition. Block Shop’s scraps and “seconds” are currently used to make pouches, non-medical grade protective masks, robes, and paper.
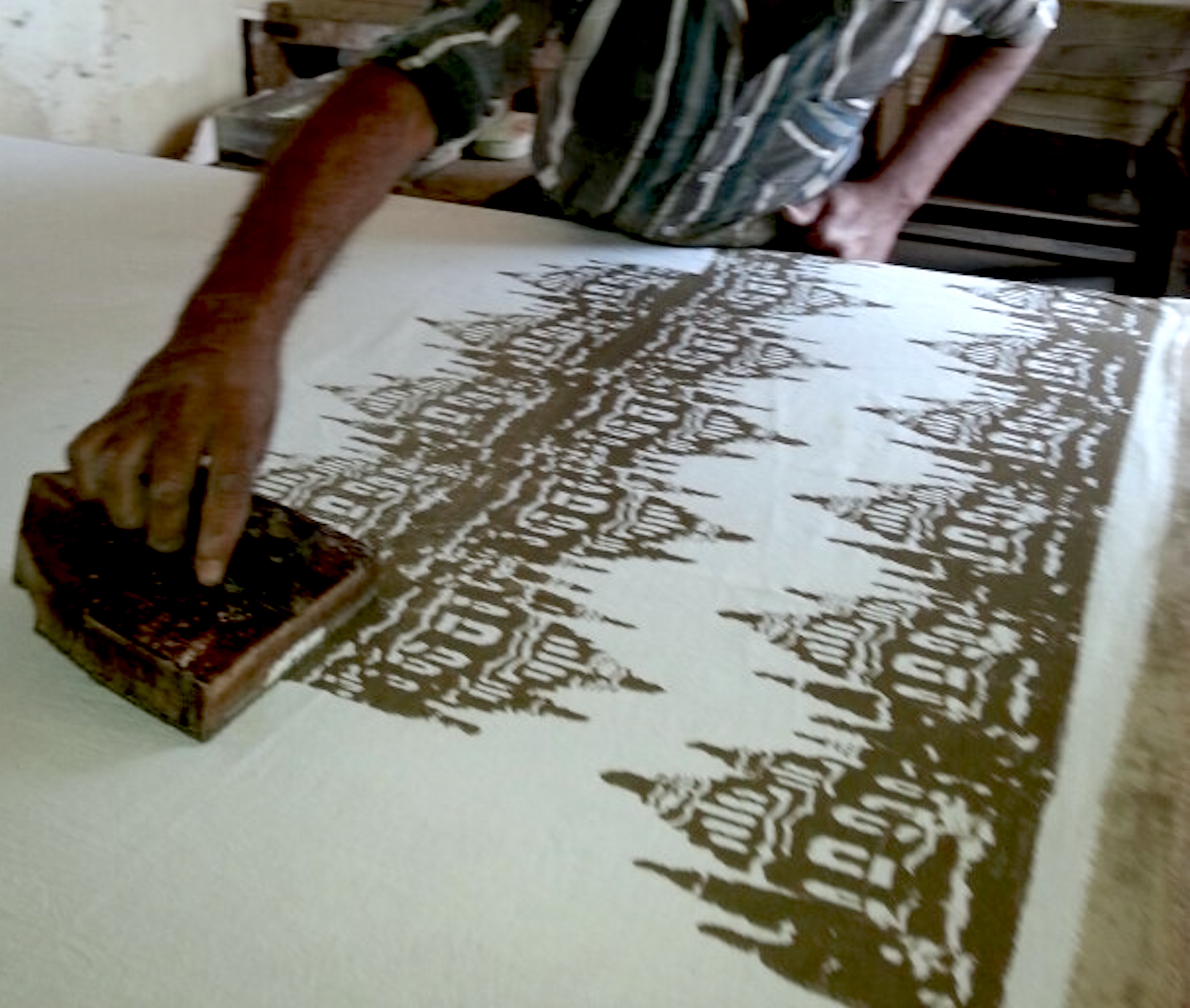

Most people can learn to block print if they have access to the correct materials and instructions. The most common form of block printing is called relief printing, and it entails cutting a design into a block of wood, linoleum, or another material. The inked block is pressed onto the material, transferring the design to the elevated portions. Like linoleum, rubber is a soft and easily carved surface for block prints. Typically they are small and mounted on wooden blocks or handles. This is the oldest type of block printing, with the images carved out of a solid piece of wood.
If your fabric is too big for that, find a flat place where you can lay out your project to dry, undisturbed. Put your prints in a safe space where they won’t be disturbed or jumped on by any small animals (the last thing you want is your cat covered in oil paint, trust). Rubber blocks are soft, easy to carve, AND easy to come by, online or in stores. Linoleum blocks are also great for their own reasons, but for my purposes, rubber works better and faster. A lot of times you’ll have to work through the not so good ideas before you eventually land on something you like. On the other hand, I am a HUGE sucker for layering prints, so maybe just do whatever the heck you want ;).
Paper artist Lisa Lloyd explores the flow of emotions in dazzling new foil block printed sculpture - Creative Boom
Paper artist Lisa Lloyd explores the flow of emotions in dazzling new foil block printed sculpture.
Posted: Mon, 09 Oct 2023 07:00:00 GMT [source]
This separates it from other printing techniques, which use many different blocks to produce a similar effect. Block-out printing is a unique screen printing method used primarily on dark colored fabrics. The process of block-out printing consists of laying a thin coat of a rubber-like substance on top of the fabric in order to “block-out” the colors lying beneath it. Dark fabrics are difficult to print on, and therefore this method is often required. Draw the quilt-inspired block printing design onto the Speedycarve block using a pencil so you can correct any mistakes.
He frequently uploads videos to his YouTube channel and streams on Twitch several times a week. Burn-out Printing is a screen printing method that lightly burns certain portions of the fabric in order to achieve a particular design. This method is often used in order to achieve a mildly transparent look on certain segments of the design. Burn-out printing is only possible on polyester-cotton or polyester-rayon blends.
Now for the fun part, and that is applying the stamp to your fabric. Your block stamp has chalk paint on it so now simply stamp it straight down on the fabric. Evenly press on the block so the design touches the fabric on all corners and such then pull it straight up. You want to use enough pressure to ensure paint transfer but not so much pressure it smears.
While not strictly necessary, a printing press can greatly facilitate and standardize the printing process. You may also require cleaning solutions, registration guides, and transfer paper, although this will depend on the specifics of your job. When it comes to block printing on fabric, India is one of the most famous sources of fine artisan patterns. The technique is largely the same, but due to a long history and specialization in different types of dyes and fabrics, the Indian subcontinent is where the craft truly shines.
No comments:
Post a Comment